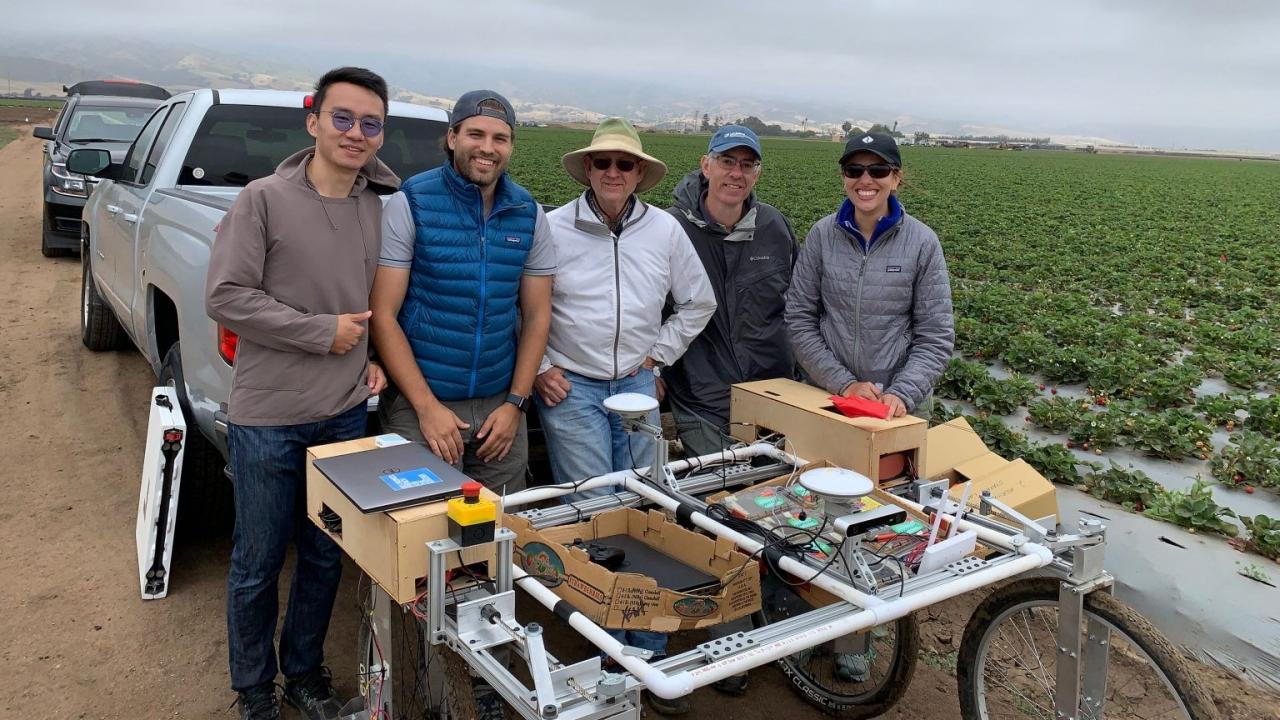
Solving agricultural challenges with engineering and robotics
By Rachel Steere, originally posted by UC Davis Engineering.
From creating fragile crop harvest-aiding mobile robots (FRAIL-bots) for strawberry harvesting to developing an automated robotic orchard platform designed to optimize fruit pickers’ performance, Stavros Vougioukas is addressing agricultural challenges and making an impact on California agriculture.
In fresh market fruit production, harvesting is one of the most labor-intensive operations, incurring high cost and dependence on a large seasonal semi-skilled workforce, which is becoming less available.
Vougioukas’ work in agricultural robotics, mechanization and automation for specialty crops has resulted in improved systems through the design, development and testing of actuators, sensors and control systems for optimal management of inputs and products.
“There are so many things that are cool about working with robotics and engineering. The feeling of seeing a complicated system actually work in the field years after writing a proposal and putting ideas together is extremely satisfying,” said Vougioukas, associate professor in the UC Davis Department of Biological and Agricultural Engineering (BAE).
In 2012, Vougioukas received a National Science Foundation (NSF) grant from the U.S. Department of Agriculture (USDA) as part of the National Robotics Initiative to help fund a four-year project devoted to the development of FRAIL-bots to increase harvesting efficiency by reducing the time to transport fruit-filled containers. Vougioukas and his team were successful in building the strawberry harvesting bots, which remain on campus awaiting extended testing.
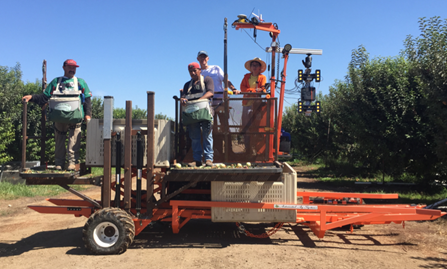
In 2016, he received an additional NSF grant from the USDA as a part of the National Robotics Initiative to develop a robotic orchard platform to increase harvest efficiency by optimizing a fruit picker’s speed and performance.
Standard orchard platforms are already commercialized and have replaced ladders to increase efficiency. Using ladders adds time for pickers when they need to change positions or empty their bag of fruit. Although eliminating ladders improved harvesting efficiency by reducing the amount of travel and climbing, there was still non-uniform fruit distribution and fruit picking at varying speeds.
“The idea was if we knew in advance the distribution of fruit on the trees and if we measured the individual picking speed of each person, then we would know how much demand there is for fruit-picking labor,” said Vougioukas. “From there, we could measure how much supply of labor there is and create a computer program that reads this information to maximize the overall efficiency and picking speed.”
Vougioukas and his team at UC Davis led this initiative and collaborated with Carnegie Mellon University. The Carnegie Mellon team, led by Dr. George Kantor, developed a 3-D camera and software to detect and localize fruits. The UC Davis team developed all the platform-related hardware and control software, the picking bag instrumentation and the integration.
Vougioukas’ colleague Dennis Sadowski, a research and development engineer in the BAE department, was the lead design engineer on the team. He repurposed a standard platform by retrofitting it with hydraulic cylinders to lift the pickers independently. They also installed a speed control system to regulate the speed and height of each individual hydraulic cylinder. BAE Ph.D. student Zhenghao Fei was also on the team and developed electronics and software to control the cylinders and speed of the platforms. He also developed special bags with sensors that measured in real time how fast the picker collected fruit.
“With camera-based sensing to estimate the distribution of fruits in front of the machine, instrument conventional picking bags to measure the harvesting speed of each picker and the use of an intelligent algorithm to control the platform’s speed and height of the lift, we were able to maximize performance,” said Vougioukas.
After running multiple experiments, the team was successful in creating a functional robotic orchard platform and found that they achieved up to 25 percent faster harvesting speeds compared to the standard non-automated platform.
“When your product actually achieves what you were hoping to achieve – it’s faster, it’s better, it’s safer – it is very satisfying because it has a real impact,” said Vougioukas. “In engineering, I want to develop things that are practical and that will work in the field. All of the brainstorming and interaction with students and colleagues is really fun. It is all very exciting and is what I enjoy most.”
Vougioukas is currently working on a new project from the National Robotics Initiative to develop a multi-arm fruit harvesting robot. The plan is to use the robotic orchard platform as a mobile unit to carry the new system that his team will develop in the next few years.